Detailed Product Description
Overview
Metis P1 permanent magnet flaw detector is a small portable inspection tool that can perform magnetic particle inspection without using a power source. This inspection tool can be used in the workshop or in the laboratory. It is more suitable for testing in environments where there is no power supply or in an explosive environment with special electrical equipment.
Technical Performance
1. Lifting power: >18KG
2. the pole distance: 50 ~ 200mm continuously adjustable
3. Dimensions: 170 mm×150 mm×32 mm
4. Yoke weight: 1.88KG
5. Packing weight: 3.5kg, Packing size: 300X250X150mm
Principle
Using the strong magnetic field of the permanent magnet, magnetize the work of the ferromagnetic material to be detected, form a local magnetic pole on the surface of the workpiece or near the surface defect, and apply magnetic powder with good magnetic permeability on the working surface, which will be attracted by the local magnetic pole and piled up on it. , thus showing the location and shape of the defect.
Structural Characteristics
The pole spacing is adjustable from 50 to 200 mm, and the probe can be rotated to detect defects in different planes. Large workpieces can be partially magnetized in sections, which is convenient for on-site operation and superior to high-altitude and inconvenient live operation.
Method of Use
1. Attention
(1) It is strictly forbidden to strike, in order to prevent the disorder of the magnetic domains, weaken the magnetic properties and affect normal work;
(2) Do not approach strong magnetic objects to prevent reverse magnetization of the instrument;
(3) After the use, fill the two yokes with a short iron to make it a loop. Reduce the interference of the earth's magnetic field and the external magnetic field.
2. Operation
(1) Prepare the work before the flaw detection, remove the iron filling, and test the lifting force>18K before use;
(2) Check that all moving parts are in good activity;
(3) When detecting, adjust the magnetic pole spacing so that the workpiece is in good contact with the yoke. According to the process procedure of the flaw detection, the large workpiece should be partially magnetized;
(4) The flaw detector is suitable for continuous and wet flaw detection;
(5) For workpieces with a certain angle, the yoke can be in good contact with the workpiece by adjusting the two arms and the yoke to perform flaw detection;
(6) After the operation is completed, wipe the instrument clean, short-circuit the two yoke irons with iron, and put them into the toolbox.
3. Failure
(1) Insufficient lifting power:
A. Check if all parts of the instrument are in good contact, when the contact is not good. The magnetic resistance increases and the lifting force decreases. At this time, the relevant screws are adjusted to make contact with them;
B. If the contact of each component is good, the magnetism of the magnetic steel is weakened, and the instrument should be magnetized;
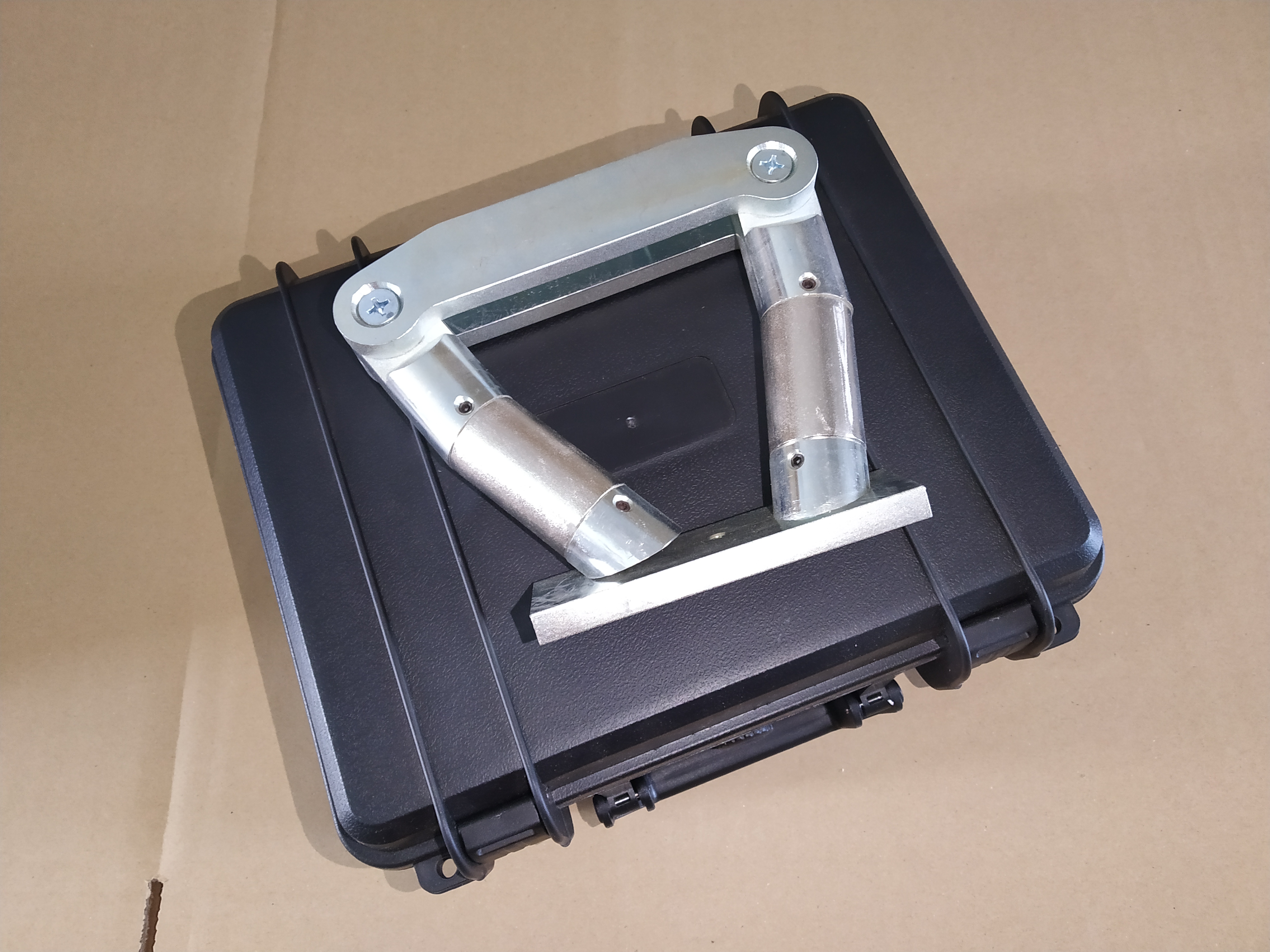
(2) When the parts are damaged, replace the parts;
(3) For normal continuous use, the flaw detector shall be inspected once in half a month, and the lifting force is >18K and the test block is 600×200×20;
(4) Magnetize the instrument periodically (as determined by the use);
(5) The magnetizing equipment can be used by the special magnetizer or flaw detector produced by us.